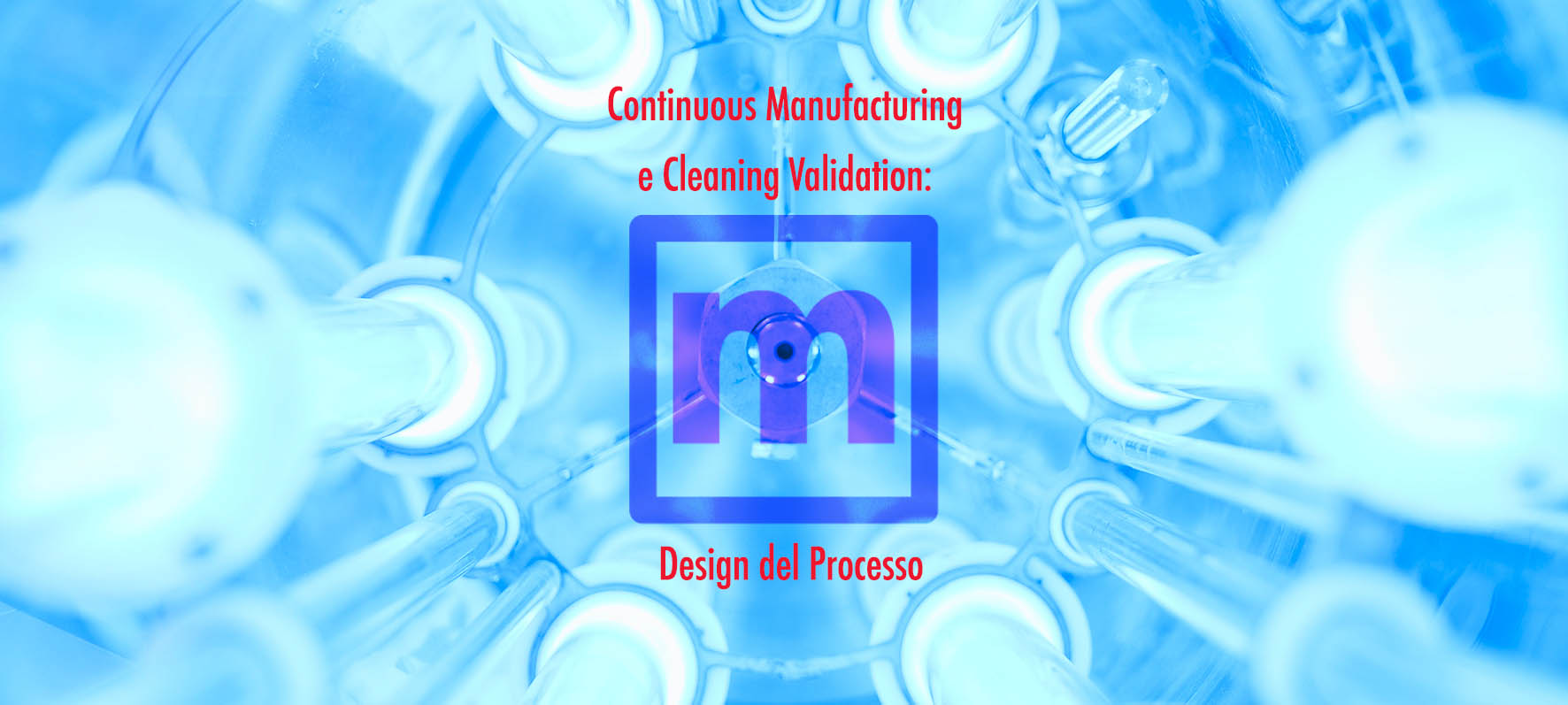
Continuous Manufacturing e Cleaning Validation: Design del Processo
Dopo 3 anni di lavoro, scrittura e consultazioni tecniche tra regolatori ed esperti dell’industria (molto più tempo se si considerano le discussioni e i rumori non ufficiali), nel corso del 2021 è programmata la conclusione della linea guida ICH Q13 “Continuous Manufacturing”. Mentre viene scritto il presente articolo è in corso l’ultimo face-to-face meeting e l’inizio della consultazione pubblica ed entro novembre la pubblicazione del testo definitivo e l’entrata in vigore.
Anche se l’abbandono del concetto di lotto in favore di processi di produzione in continuo non è mandatorio e certamente non è applicabile a tutte le realtà produttive, si tratta comunque di un passo avanti tecnologico e concettuale molto importante per l’industria farmaceutica, da sempre non proprio incline ai cambiamenti, per motivi intrinsechi ai processi e alle relative implicazioni regolatorie. Questa nuova modalità produttiva può potenzialmente portare considerevoli vantaggi alle realtà che la adotteranno, in termini di qualità e di gestione dei processi (aumentata automazione, minimo intervento manuale, controlli puntuali in linea) nonché economici (costi ridotti di qualità e manutenzione). Occorre valutare attentamente ogni aspetto del cambiamento in atto per capirne tutte le implicazioni e valutare il rapporto rischio\beneficio per prendere la giusta decisione.
Cosa aspettarsi quindi dalla convalida delle procedure di pulizia (Cleaning Validation) per le realtà che adottano il Continuous Manufacturing?
Da sempre la Cleaning Validation è un’attività onerosa per la Quality Unit (assessment, calcolo delle soglie, test e verifiche, reporting), ma indispensabile e particolarmente critica se la linea di equipment è multiprodotto a causa della cross-contaminazione. Per la produzione in batch in linee dedicate monoprodotto occorre almeno dimostrare che l’attività di pulizia è in grado di rimuovere i residui di lavorazione ed eventuali sottoprodotti, accumulati in un certo numero di produzioni consecutive (ad es. 5-10 batch, giustificato da analisi del rischio). Questo è richiesto sia dal 21 CFR (Part 211.67 “Equipment cleaning and maintenance”) che da EUDRALEX Vol.4 (Annex 15, Chapter 10 “Cleaning Validation”).
In assenza per adesso di una linea guida definitiva possiamo includere Il Continuous Manufacturing nella casistica di linee dedicate monoprodotto e convalidare la procedura di cleaning entro un certo intervallo temporale, identificato come “campagna produttiva”. Per chiarezza riportiamo qui la definizione di lotto tratta dalla direttiva 2003/63/EC:
“For the control of the finished product, a batch of a proprietary medicinal product comprises all the units of a pharmaceutical form which are made from the same initial mass of material and have undergone a single series of manufacturing operations or a single sterilisation operation or, in the case of a continuous production process, all the units manufactured in a given period of time.”
Quindi, non avendo a che fare con lotti, dobbiamo definire bene quale sia questo intervallo temporale entro il quale convalidare.
Questo, insieme agli altri fattori critici, dovrebbe essere analizzato e ben definito nell’analisi del rischio iniziale in fase di design, con metodologie e approcci descritti in ICH Q9 (HACCP, FMEA, FTA). Potrebbe essere opportuno definire mediante DoE (Design of Experiment) i parametri critici di qualità (CQA) e il range di variazione consentito, collegati ai parametri critici di processo (CPP). Nello sviluppo del metodo di cleaning il DoE è l’oggetto principale della convalida.
Sicuramente l’utilizzo della PAT (Process Analytical Technology) è caldamente suggerito nel Continuous Manufacturing, quindi anche per la cleaning, in quanto consente il monitoraggio in tempo reale dei CQA.
L’uso di tecniche PAT è quindi opportuno sia in fase di sviluppo e convalida che in fase di routine per il monitoraggio delle performance.
Strumenti quali spettrofotometri NIR, conducimetri, analizzatori TOC, sensori elettrochimici, biosensori, ecc. installati nella linea produttiva monitorano continuamente i CQA (es. residui organici, concentrazione di sottoprodotti di degradazione, ecc.) e sono direttamente correlabili ai residui di sostanza attiva o di particolari eccipienti. In generale possiamo dire che metodi di analisi aspecifica (es. pH, conducibilità, TOC, UV-vis) sono preferibili a metodi specifici per semplicità di uso, sicurezza e incontestabilità del risultato. Se proprio dobbiamo usare un metodo con elevata specificità preferiamo quelli con efficienza elevata e tempi di analisi ristretti (es. UHPLC contro HPLC tradizionale).
Per quanto riguarda il campionamento sono preferibili metodi in linea, che non prevedano l’accesso diretto e disassemblaggio degli equipment con discontinuazione del processo (es. tecniche di rinse sono preferibili a swab).
Il sistema di cleaning di elezione sarà basato sul metodo CIP (Cleaning In Place), ormai da tempo adottato come standard nell’industria, che ha soppiantato completamente i metodi di manuali in quanto presenta numerosi vantaggi, tra cui: disassemblaggio parti non necessario, aumentata automazione con intervento manuale minimo o nullo (diminuito errore umano), aumentata efficienza e consistenza delle performance e affidabilità del processo, convalida più semplice.
Il design degli equipment può aiutare e deve essere pensato per facilitare il passaggio della soluzione di lavaggio durante la fase di cleaning.
Questo per riduzione gomiti e angoli, superfici rugose, punti ciechi, pendenze. Con un design adeguato è possibile minimizzare l’uso di detergenti e antibatterici, acqua di lavaggio e perdite di soluzione, nonché le tempistiche del processo.
Una volta affrontati gli aspetti di design del processo di cleaning dobbiamo pensare alle fasi di qualifica e mantenimento dello stato di convalida nell’ottica di un approccio completo di Lifecycle Management. Questi aspetti includono manutenzione preventiva, change control e CAPA management, periodic review e monitoraggio continuo. Meritano un approfondimento a parte in un prossimo articolo.
Tag
Share
STAY IN THE LOOP
Iscriviti alla nostra newsletter.
[mailup_form]
La revisione dell’Annex 1 Manufacture of Sterile Medicinal Products delle GMP fu finalizzato ad agosto 2022 dalla Commisione Europea. Dopo […]
Sistema Qualità. Se la tua azienda subisse un controllo oggi, ti sentiresti davvero al sicuro? La qualità è cruciale nell’industria […]